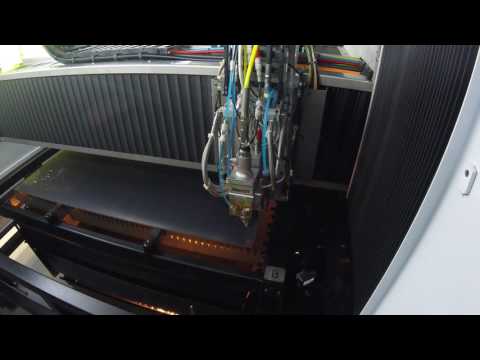
The cutting head on the 12-kilowatt plate laser is a sealed unit. To handle 12,000 watts of the laser power, Whitney uses a reflective cutting head. Reflective cutting heads use specialty ground copper mirrors to replace the collimating and focusing lenses. Copper mirrors are internally cooled, allowing cooling to take place much more efficiently, eliminating prospective hot spots from contamination. With direct cooling, the mirror surface does not thermally distort. Transmissive optics, on the other hand, use lenses instead of mirrors. Lenses are cooled from the edges, yet the beam goes through the center of the lens. So when using high-power – 6000 watt and above – even the slightest contamination within the beam cap on the a lens will create a hotspot, causing distortion of the lens and a resultant shift in the focal point. This in turn yields unacceptable cut quality or cutting head failure.
Whitney’s state of the art cutting head for 6-kilowatt cutting is a shop-hardened cutting head that can be serviced onsite. Competitors cutting heads require expensive, off-site servicing. This can result in excessive downtime and logistics issues, as well as an expensive spare cutting head for backup.
Whitney cutting heads include intelligence and monitoring. Built-in sensors within the cutting head monitor temperatures in all critical areas. This monitor is integrated into the CNC control, which will stop cutting if temperatures reach predefined levels.
These are just a few of the features of the Whitney 12-kilowatt plate laser. For more information, give us a call or check out our website.