LASER Power Needs Assessment
CNC Fiber LASER: How Much Power Do I Need?
a simple laser power needs assessment
We can begin to answer this question by discussing the three cutting processes available with fiber LASER cutting, and which ones you want to use for the materials you wish to cut. The three processes are defined by the gas used to cut – Nitrogen, Air, or Oxygen.
CNC LASER Power Assessment
Fiber LASER cutting is capable of extremely fast cutting speeds. In order to take advantage of those cutting speeds, however, the use of high pressure Nitrogen or clean, dry compressed air are required. Cutting with Oxygen can be done on all carbon steel, however the cutting speeds using Oxygen are significantly slower than with Nitrogen or compressed air.
In general, Nitrogen assist gas produces the best quality cuts and provides that fastest cutting speeds. Nitrogen does not react with the cut edge surface of the workpiece, so the finished edge is shiny, and free of oxidation. If the finished part will be powder coated in a later operation, then Nitrogen offers the best condition for powder adherence without additional surface preparation. Since Nitrogen does not react with the workpiece, it is used strictly as an ejection gas for the molten material heated by the LASER beam. This makes the Nitrogen cutting process the most stable of the three gases. The power/speed ratio is almost linear, and extremely fast cutting speeds are possible simply by adding more power. However, in order to do its job effectively, Nitrogen has to be delivered at high pressures – usually around 200psi or sometimes more. Furthermore, thicker materials require larger diameter nozzles to be used (to enable the molten material to be ejected from the cut properly). This consumes a tremendous amount of Nitrogen and can be very costly to the end user – sometimes in excess of $100,000 annually depending upon nozzle sizes used. There are also thickness limitations of the Nitrogen cutting process. For example, a 6 kW LASER can generally cut up to ¼” thick carbon steel, while a 2 kW LASER is limited to around 10 ga (0.135”).
Air assist gas is similar to Nitrogen cutting, although slightly more reactive with the workpiece. High cutting speeds are possible – approximately the same as Nitrogen. However the finished edge quality is not as shiny as with Nitrogen and typically requires additional surface preparation if the final product has to be powder coated. Furthermore, the maximum material thickness which can be processed is thinner than with Nitrogen. Air cutting requires a separate air compressor capable of producing pressure higher than normal shop air, and also requires extremely high filtration to eliminate the possibility of contaminant migration to the cutting head. Compressors and filtration capable of supporting air cutting will add several thousand dollars to the price of the machine. However, ongoing operating cost is reduced as you do not need to purchase cutting gas (Nitrogen or Oxygen) to run the LASER (although filters need to be replaced regularly to avoid contamination of the cutting head). Air cutting is typically limited to slightly thinner materials than Nitrogen cutting.
Oxygen assist gas is different from Nitrogen and Air cutting in that the heat is generated by the reaction of the Oxygen with the steel base metal. It is primarily used for carbon steel cutting – not for stainless steel or aluminum (it is also sometimes used for cutting copper). A minimum threshold of heat is required to create the gas/metal reaction between Oxygen and Iron to create an exothermic reaction. This is very similar in principle to using an oxyacetylene torch – the LASER heat acts as a catalyst to create a chemical reaction between the Oxygen and the steel. Once the heat is established, cutting takes place. Because the process is more related to a chemical reaction instead of LASER heat, additional power is normally not necessary or even helpful and may only result in minimal speed improvements. Cutting speeds in thinner material are significantly slower than cutting with Nitrogen or air. While high power is not required for cutting most material thicknesses, it can be advantageous for piercing heavier material. For example, it is possible to cut ¾” carbon steel at 22 inches/minute* with only 2kW of power. However, it takes more than 20 seconds to pierce (start the cut). A 4 kW LASER will cut the same ¾” piece of carbon steel at 30 inches/minute*, but it can pierce it in only 2 seconds. Not only will the 20 second pierce add significant time to the production of the part, it will also limit the minimum hole size due to the large amount of heat added into the material while piercing. Steel up to 1” thick can be cut with Oxygen.
The differences can be shown, in general, in the following table. Specific differences in cutting speeds, power requirements, and operating cost are best reviewed with the manufacturer.
Nitrogen |
Air |
Oxygen |
|
Cut Quality | Best. Shiny cut surface without any oxide layer; Good corner definition | Generally very good, but with a slight oxide layer on the cut surface; Good corner definition | Very Good, but with an oxide layer on the cut surface; Sharp corners may exhibit overburns |
Cutting Speeds | Extremely fast – limited by machine design (acceleration) | Extremely fast – limited by machine design (acceleration) | Limited – chemical reaction of Oxygen and steel limits realistic maximum speeds to around 300 ipm in thin materials |
Material Types | All (Carbon steel is limited in thickness) | Carbon steel; Copper in some cases | |
Powder Coat Prep | No prep required | Chemical or mechanical oxide layer removal required | Chemical or mechanical oxide layer removal required |
Operating Cost | Very high due to large Nitrogen consumption; Can be mitigated by purchasing Nitrogen generator | Low – mostly from filter replacements and electrical power for air compressor | Low – Oxygen used at low pressures, so consumption is relatively low |
Capital Cost | Medium (Purchase or lease bulk Nitrogen system and distribution lines); Or High (purchase Nitrogen generator) | Medium to High (purchase high capacity air compressor with filtration | Low |
Power Requirements | Directly related to material thickness; high power yields greater thickness capacity and faster cutting speeds | Directly related to material thickness; high power yields greater thickness capacity and faster cutting speeds | Lower power requirements. Higher power is beneficial for faster piercing but not required |
With the understanding of the three processes, we can now answer the “power question” using the following charts. The cutting speeds assume that all materials that can be cut with Nitrogen (or Air) will be cut with them since Nitrogen (and Air) yield the fastest cutting speeds and best quality.
Chart 1 – Process Capability – Carbon Steel
1kW | 1.5kW | 2kW | 2.5kW | 3kW | 4kW | 5kW | 6kW | 8kW | 12kW | |
0.036 | N2/Air | N2/Air | N2/Air | N2/Air | N2/Air | N2/Air | N2/Air | N2/Air | N2/Air | N2/Air |
0.048 | N2/Air | N2/Air | N2/Air | N2/Air | N2/Air | N2/Air | N2/Air | N2/Air | N2/Air | N2/Air |
0.060 | N2/Air | N2/Air | N2/Air | N2/Air | N2/Air | N2/Air | N2/Air | N2/Air | N2/Air | N2/Air |
0.105 | O2 | O2 | N2 | N2/Air | N2/Air | N2/Air | N2/Air | N2/Air | N2/Air | N2/Air |
0.120 | O2 | O2 | N2 | N2 | N2/Air | N2/Air | N2/Air | N2/Air | N2/Air | N2/Air |
0.135 | O2 | O2 | N2 | N2 | N2 | N2/Air | N2/Air | N2/Air | N2/Air | N2/Air |
0.187 | O2 | O2 | O2 | O2 | O2 | N2 | N2 | N2/Air | N2/Air | N2/Air |
0.250 | O2 | O2 | O2 | O2 | O2 | O2 | N2 | N2 | N2 | N2/Air |
0.312 | O2 | O2 | O2 | O2 | O2 | O2 | O2 | O2 | N2 | N2 |
0.375 | O2 | O2 | O2 | O2 | O2 | O2 | O2 | O2 | O2 | N2 |
0.500 | N/A | O2 | O2 | O2 | O2 | O2 | O2 | O2 | O2 | N2 |
0.625 | N/A | N/A | O2 | O2 | O2 | O2 | O2 | O2 | O2 | O2 |
0.750 | N/A | N/A | O2 | O2 | O2 | O2 | O2 | O2 | O2 | O2 |
1.000 | N/A | N/A | N/A | N/A | N/A | N/A | O2 | O2 | O2 | O2 |
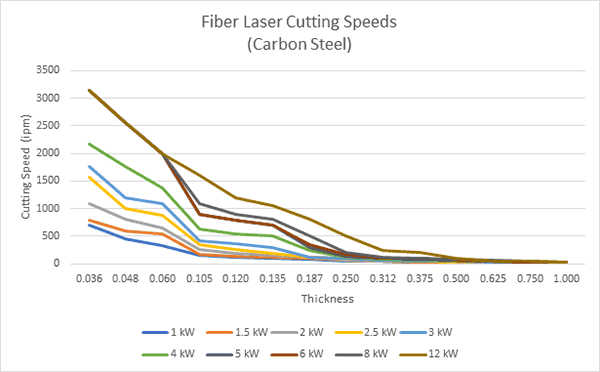
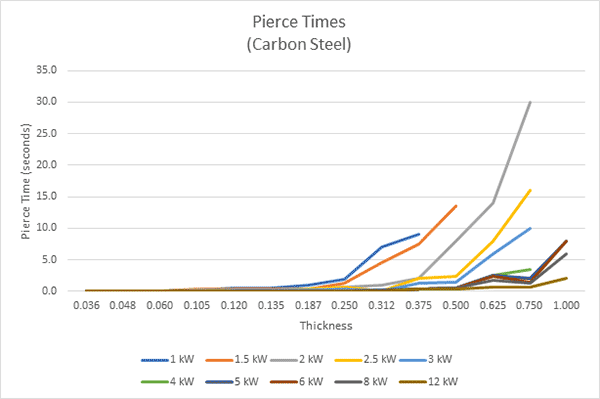
The graphs show that cutting speed is impacted more significantly by power in thinner material, while pierce time is impacted more significantly by power in thicker material.
Using the above information, the following guide can help steer you to the best decision:
- What are the thinnest and thickest materials (of each material type) you must LASER cut? The power level needs to be capable of producing the entire range of materials. Look at Chart 1 to make sure the power level is appropriate for cutting these parts.
- How important is speed? If you plan to run the LASER at full capacity (full shifts of work) speed may be more important than if you have a limited amount of work for the machine and the machine will regularly sit idle.
- If cutting speed is important, which materials/thicknesses comprise the most common materials you plan to cut? These materials should be cut as efficiently as possible (Nitrogen or Air cutting if available). Review the cutting speeds for these parts and see if additional power will be meaningful in your “sweet spot”
- Do your parts have a lot of internal holes? If so, is a substantial amount of your hole-intensive work in material thicker than 7 ga steel (4.5mm)? If so, higher power yields faster pierce times.
- Will your parts be powder coated after cutting? Significant savings can be achieved by cutting these parts with Nitrogen. Look at Chart 1 to make sure the power level is appropriate for Nitrogen cutting these parts.
Fabrication Equipment
Thermal Cutting Machines
Contact Piranha
- 650 Race St.
Rockford IL 61105, USA - Toll Free: 800-338-5471
- Local: 815-964-6771