The Whitney 3400HEAVY Combination Machine Tool uses the fastest technologies to make parts – Punching and Plasma Cutting.
- Punched holes provide accurate internal features.
- It is faster to punch holes than to pierce and contour holes with plasma or laser.
- External features are plasma cut. Advanced plasma-cutting technology provides highly productive contouring (much faster than laser) with high quality.
- Small kerf angle (vertical cuts)
- Dross-free cutting
- Additional features such as forming (countersinks, tread plate, louvers), drilling and tapping can be added to eliminate additional downstream operations, allowing parts to be completed in a single operation.
Manufacturing costs are lower using the combination machine technology.
- Labor costs are lower because it takes significantly less time to manufacture the parts.
- Operating costs are lower.
- Amortization of capital costs is significantly lower since
- Lower initial capital cost than laser
- Faster cycle time – Cost of capital per fabricated part is lower because capital costs are amortized over more fabricated parts.
The PROFIT-DOUBLER
- Higher profit per part —lower overall cost per piece gives a higher profit margin per piece.
- More parts generating profit—more parts are produced (in the same amount of time) on a combination machine, so there are more parts generating profit than on the other technologies.
SPECIFICATIONS OF MODEL 3400HEAVY
|
INCH |
METRIC |
PUNCHING FORCE |
55 Tons |
500 kN |
MATERIAL THICKNESS |
|
|
Minimum |
.060″ |
1.5 mm |
Maximum |
.750″ |
19.0 mm |
MAXIMUM PUNCH DIAMETER |
5.000″ |
127 mm |
PUNCHING CAPACITY A36 (60ksi / 410 MPa Shear Strength) |
|
.250″ (6 mm) |
5.000″ (shear) |
127.0 mm (shear) |
.375″ (10 mm) |
3.234″ (shear) |
82.1 mm (shear) |
.500″ (12 mm) |
1.938″ (shear) |
49.2 mm (shear) |
.625″ (16 mm) |
1.234″ (shear) |
31.3 mm (shear) |
.750″ (19 mm) |
0.766″ (flat) |
19.5 mm (flat) |
PUNCHING HIT RATE |
125 HPM |
10 gage (3 mm) material punched on 1″ (25.4 mm) centers |
|
|
|
MAXIMUM POSITIONING AREA |
|
|
X-axis |
190.6″ |
4842 mm |
Y-axis |
80.7″ |
2050 mm |
NOMINAL BLANK SIZE |
|
|
Without Auxiliary Tables |
80″ x 160″ |
2m x 4m |
The 3400HEAVY can punch and plasma cut a full 80″ x 160″ (2m x 4m) sheet of material without repositioning. |
EXTENDED BLANK SIZE |
|
|
With Auxiliary Tables and Repositioning |
80″ x 320″ |
2m x 8m |
Longer plates may be accommodated in certain applications using multiple automated repositioning cycles. These applications must be reviewed by W. A. Whitney. |
POSITIONING SPEED PER AXIS |
1,200 in/min |
30 M/min |
POSITIONING ACCURACY |
±0.005″ |
±0.13 mm |
MINIMUM PROGRAMMED INCREMENT |
0.001″ |
0.01 mm |
MAXIMUM MATERIAL WEIGHT |
3,000 # |
1,360 kg |
MAXIMUM BLANK SIZE |
|
|
Without Auxiliary Tables |
80″ x 144″ |
2000 x3500 mm |
Longer plates may be accommodated in certain applications using automated repositioning. These applications must be reviewed by W. A. Whitney. |
|
|
|
APPROXIMATE SHIPPING WEIGHT |
|
|
Base Machine & Accessories |
45,000 # |
20,250 kg |
Optional accessories will increase overall shipping weight. Largest component weight is less than 35,000#/ 15,875 kg |
|
|
|
FOUNDATION REQUIREMENT |
|
|
An 8″ / 200 mm reinforced concrete foundation is required beneath the press frame. See specific foundation requirements. |
|
|
|
ELECTRICAL REQUIREMENTS |
|
|
460/3/60 |
125 KVA |
Contact W. A. Whitney for voltages other than 460/3/60 |
|
|
|
APPROXIMATE FLOOR SPACE |
|
|
Front – Back |
288″ |
7,316 mm |
Left – Right |
355″ |
9,017 mm |
Height – Machine |
100″ |
2,527 MM |
Height (w/ dust collector) |
136″ |
3,473 mm |
Base machine and required accessories only. Actual floor space and height requirements can vary with options. Contact us for detailed floor space requirements. |
NOTE: Specifications are subject to change without notice.
ACCESSORIES
- Tool Caddy Tooling Expansion System
- Ink Jet Part Marking System
- Pneumatic Tapping System
- Pneumatic Combination Drilling/Tapping System
- 10HP Servo Controlled Combination Drilling/Tapping System
- 30HP Servo Controlled Combination Drilling/Tapping/Milling system with tool changer
- Bevel Plasma Cutting Plasma Assembly
- Small Parts Conveyor
- PlatePARTNER Semi-Automatic Loading System
- PlatePARTNER Gantry Automatic Loading System with available material storage system
- Skeleton Removal Table
- Auxiliary Ball Transfer Tables
INCLUDED EQUIPMENT
This proposal describes the Model 3400HEAVY Fabricating Center, 55 ton (500 kN) capacity, 100″ x 160″ (2.5m x 4.0m) positioning area, per attached specifications, for 460/3/60 volt incoming power. (NOTE: Material blank sizes greater than 160” can be processed by utilizing the Programmable Repositioning Assembly.)
Siemens 840DSL CNC 3-Axis Positioning / Contouring Control including:
- Pendant mounted operator’s station,
- Windows 10 Operating System,
- Alpha/Numeric panel and Windows keyboard with trackball
- 5 MB part program and system shared memory
- USB Interface
- 15″ High Resolution Color LCD Monitor.
Network Card, installed in the CNC Control, including:
- 10/100 Mb RJ45 Ethernet
- Ready for connection to customer’s existing Network
- Suitable for downloading Part Programs
Automatic Tool Changing, accomplished with a tool cartridge mounting system mounted to the X-axis Rail with a total of (12) slots available for tooling cartridges. The Tooling System uses Whitney 36TC Style Tools, and includes one (1) Alignment Tool Set.
Programmable Small Parts Drop Door, 24″ x 72″, (600 mm x 1830 mm), located immediately next to the plasma torch, used for automatically unloading small parts and cut-outs. A sensor detects the passage of a finished part through the drop door. For reliability purposes, the sensor confirms that the part passes through the door before the machine is released to proceed to the next move, and for productivity reasons, the sensor also triggers the door to close as soon as the part passes. Average drop door cycle time is only 2.5 seconds.
Hypertherm MAXPRO200®, LongLife® air and oxygen plasma cutting system with impressive cutting speeds, consistent cut quality, and exceptional consumable life.
Integrated Dust Collection System, including the dust collector, spark trap, duct, wiring, and interconnections are provided.
NOTE: The supplied dust collection system is designed for plasma cutting steel and stainless steel. Plasma cutting aluminum requires an optional additional aluminum dust collector.
Integrated Plasma System Support Equipment:
- Air intensifier for increasing shop air pressure as required for plasma cutting
- Slag Chamber lined with refractory materials
Whitney Halo, plasma torch collision detection device.
Hydraulic Work Clamp Assembly, including (2) standard work clamps for up to 3/4″ (19 mm) thick material. Protection is provided by a clamp verification cycle in the CNC Control. This ensures proper physical location of the work clamps relative to the values in the CNC control. Retractable reference stops are included which allow parts with camber (up to 1.00″ / 25 mm) to be processed without interference during automatic repositioning.
Programmable Repositioning Assembly is designed to relocate the work clamps on the material in order to process areas of the material that are within the work clamp safety zones. Automatic repositioning allows the repositioning of material blanks which are longer that the X-axis.
NOTE :If the machine will be making finished parts longer than the X-axis length, please contact us to review the specific application.
Material Support Roller Tables are supplied for the left and right side of the machine.
NOTE: The material support roller tables are designed to support the material during processing. For applications in which the material thickness is predominately 0.125” (3 mm) or less, ball transfer support tables are recommended in lieu of the roller tables.
Hydraulic Pressure Switch Circuit, selectable through part program, for ram reversal upon pressure. This allows forming work such as center punch marks, number stamps, countersinks, louvers, and embossing to be done.
Programmable selection of punch/stripper height to allow for mill tolerance bowed material and forming tools. Bowed material must be loaded with the bow up.
Hydraulic Power Unit, with 40 H.P. (30kw) drip-proof motor and hydraulic oil.
Automatic Punch Lubrication, with reservoir.
Remote Diagnostics Package – allows many machine problems to be diagnosed via the Internet using TeamViewer. W. A. Whitney Service Technicians can log directly onto the CNC control for the purpose of diagnosing problems, reviewing NC programs, downloading new software, and changing parameters if required. Customer is responsible for providing a suitable Ethernet connection at the machine CNC control with Internet access. A telephone line or cell phone is recommended so that the technician can talk to the operator/maintenance person while diagnosing the problem.
Software License for all software resident on the CNC Control. The software is proprietary, and the intellectual property of W. A. Whitney Co. Prior to the commissioning of the machine tool, the user must sign a software license agreement. This is a non-transferable license that must be renewed by any and all subsequent owners of the machine tool. The value of this software license is $1,500.00, and it is included in the price of the machine.
Operating and Service Manual consisting of (1) print copy and (1) CD copy W. A. Whitney Documentation and (1) print copy of Vendor Documentation including Siemens CNC and Drives.
Electrical Standards – The machine conforms to W. A. Whitney electrical design standards which are based on N. E. C., NFPA-79, and UL Standards with deviations. Components are NEMA and IEC rated where possible.
55 TON PUNCHING CAPACITY
IMPORTANT NOTE: Punching of high tensile material is a special application for Whitney Combination Machine Tools and may void the machine warranty and cause premature tooling wear. High tensile strength material is defined as any material whose tensile strength is greater than 60ksi (413 MPa). Materials often referred to as “remnants” or “seconds” will often randomly exhibit tensile strength greater than 60ksi (413 MPa) and thus will void the machine’s warranty. WHITNEY reserves the right to have a representative sample of customer supplied material mechanically and/or chemically tested. If processing high tensile material, please consult the factory for a review of your specific requirements. In some cases, a larger Whitney Combination Machine model could be recommended.
The 55 TON PUNCHING CAPACITY allows the 3400HEAVY to:
- Punch larger hole sizes in a given material type and thickness
- Punch holes in higher tensile strength materials
- Punch thicker materials
3400HEAVY INCLUDED TOOLING CARTRIDGE AND ADAPTERS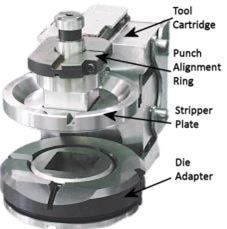
Each Punch and Die Tooling station requires (1) Tooling Cartridge and (1) Tooling Adapter Assembly. Each complete tooling station assembly includes following components:
- (1) Tooling Cartridge
- (1) Punch Alignment Ring
- (1) Stripper Plate
- (1) Die Adapter Max. 4″ I.D. Dies.
A total of (12) punching stations can reside in machine at one time. The following components are included with the 3400HEAVY:
(12) Tooling Cartridge and Adapter Assemblies
- (6) 1-1/4″ (32 mm) O. D. Tooling Adapter Assembly
- (3) 2-1/8″ (54 mm) O. D. Tooling Adapter Assembly
- (2) 2-3/4″ (70 mm) O. D. Tooling Adapter Assembly
- (1) 3-3/4″ (95 mm) O. D. Tooling Adapter Assembly
- (12) Tooling Cartridges
- (12) Punch Alignment Ring
The final selection of Tooling Adapter Assemblies may vary with each application.
MAXPRO200® PLASMA CUTTING SYSTEM (STANDARD)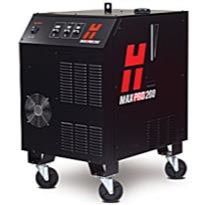
The MAXPRO200® Plasma Cutting System, standard on the 3400HEAVY, offers LongLife® air and oxygen plasma technology, giving high quality plasma cuts with excellent consumable life. The MAXPRO200® plasma system incorporates the superior cut quality of oxygen plasma cutting with increased cutting capability and reliability.
Advantages include:
- Little or no dross on plasma cut edges
- Narrow kerf width for fine detail cutting
- Long consumable life with high system reliability
- Faster cutting speeds with best edge quality
The MAXPRO200® system includes:
- MAXPRO200® Plasma Power Unit
- Quick Change plasma torch and positioning assembly for correct stand-off height
- Dust collector with filters and spark trap
- Slag collection system
Cutting Speeds
The published values for the MAXPRO200® Plasma Cutting System represent the speeds attainable under controlled conditions. The practical speeds for processing carbon steels are shown in the following chart and are the optimum production values for minimum set-up time and best quality cuts. Cutting Speeds – MAXPRO200® – Mild Steel – O2 / Air
|
.075″ 2.0 mm |
.135″ 3.0 mm |
.187″ 4.0 mm |
.250″ 6.0 mm |
.375″ 10.0 mm |
.500″ 12.0 mm |
.625″ 15.0 mm |
.750″ 20.0 mm |
50A |
220 ipm 3050 mmpm |
130 ipm 3650 mmpm |
85 ipm 2800 mmpm |
65 ipm 1750 mmpm |
|
|
|
|
130A |
|
240 ipm 5900 mmpm |
190 ipm 5325 mmpm |
150 ipm 3925 mmpm |
110 ipm 2680 mmpm |
80 ipm 2200 mmpm |
60 ipm 1665 mmpm |
50 ipm 1195 mmpm |
200A |
|
|
|
235 ipm 6210 mmpm |
150 ipm 3735 mmpm |
130 ipm 3415 mmpm |
105 ipm 2845 mmpm |
80 ipm 1920 mmpm |
Available Cutting Processes:
|
MAXPRO200® PROCESS SELECTION GUIDE
(Plasma / Shield) |
100AMP |
130AMP |
200AMP |
Steel |
O2 / Air |
Air / Air |
O2 / Air |
Air / Air |
O2 / Air |
Air / Air |
Stainless |
Air / Air |
—- |
Air / Air |
N2 / N2 |
Air / Air |
N2 / N2 |
Aluminum |
Air / Air |
—- |
Air / Air |
N2 / N2 |
Air / Air |
N2 / N2 |
|
Note: Typical preferred processes are indicated BOLD. |
Gas Requirements:
|
|
MAXPRO200® |
|
GAS TYPE |
REQ’D |
QUALITY |
SUPPLY |
Air |
✓ |
Clean, dry, oil-free (ISO 8573-1 class 1.4.2) |
90 psi ±10 psi @ 400 scfh
6.2 bar ±0.7 bar @ 11330 l/h |
Oxygen (O2) |
✓ |
99.5% pure (liquid gas recommended) |
90 psi ±10 psi @ 400 scfh
6.2 bar ±0.7 bar @ 11330 l/h |
Nitrogen (N2) |
✓ |
99.995% pure (liquid gas recommended) |
90 psi ±10 psi @ 400 scfh
6.2 bar ±0.7 bar @ 11330 l/h |
NOTE: Customer is to furnish suitable regulators for connections to included supply hoses.
HALO TORCH COLLISION DETECTION DEVICE (STANDARD)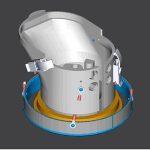
The HALO TORCH COLLISION DETECTION DEVICE detects part tip ups that collide with the plasma torch housing. If the halo detects a collision, an immediate emergency stop command is given to the CNC control to stop the machine axis motion and turn off the plasma cutting system, preventing torch replacement and down time cost.
MACHINE OPTIONS
INCREASED PUNCHING CAPACITY – 75 TON (675 kN) (OPTIONAL)
IMPORTANT NOTE: Punching of high tensile material is a special application for Whitney Combination Machine Tools and may void the machine warranty and cause premature tooling wear. High tensile strength material is defined as any material whose tensile strength is greater than 60ksi (413 MPa). Materials often referred to as “remnants” or “seconds” will often randomly exhibit tensile strength greater than 60ksi (413 MPa) and thus will void the machine’s warranty. WHITNEY reserves the right to have a representative sample of customer supplied material mechanically and/or chemically tested. If processing high tensile material, please consult the factory for a review of your specific requirements. In some cases, a larger Whitney Combination Machine model could be recommended.
The INCREASED PUNCHING CAPACITY OPTION – 75 TON (675 kN) allows the 3400HEAVY to:
- Punch larger hole sizes in a given material type and thickness
- Punch holes in higher tensile strength materials
- Punch thicker materials
The maximum weight capacity of the 3400HEAVY remains 1,800# (820 kg).
HPR130XD PLASMA CUTTING SYSTEM (OPTIONAL)
The HyPerformance Plasma HPR130XD Oxygen Plasma Cutting System option is available in lieu of the standard MAXPRO200® plasma system.
The HPR130XD incorporates the superior cut quality of HyDefinition® technology with increased cutting capability and reliability of the standard MAXPRO200®. Patented LongLife® technology improves consumable life and reduces cutting costs.
Advantages include:
- Near vertical edge quality
- Little or no dross on plasma cut edges
- Narrow kerf width for fine detail cutting
- Long consumable life with high system reliability
- Improved Stainless Steel process reduces edge discoloration
- Faster cutting speeds with best edge quality
The Whitney HPR130XD Optional package includes:
- HPR130XD Plasma Power Unit
- Automatic Gas Console
- Quick Change plasma torch and positioning assembly for correct stand-off height
- Quick disconnect torch head
- Air Intensifier
- 8 Cartridge Dust Collector with filters and spark trap
- Robust Slag Collection System
XPR170 PLASMA CUTTING SYSTEM W/ CORE™ or OPTIMIX™ CONSOLE (OPTIONAL)
The Hypertherm XPR170™ Plasma Cutting System option is available in lieu of the standard MAXPRO200® plasma system.
The XPR170™ represents the most significant advance in mechanized plasma cutting technology, ever. This next generation system redefines what plasma can do by expanding its capabilities and opportunities in ways never before possible. With unmatched X-Definition™ cut quality on mild steel, stainless steel and aluminum, the newXPR170™ increases cut speed, dramatically improves productivity and slashes operating costs by over 50%. New ease-of-use features and engineered system optimization make the XPR170™ easier to run with minimal operator intervention, while also ensuring optimal performance and unmatched reliability.
Advantages include:
The XPR170 advances HyDefinition® cut quality by blending new technology with refined processes for next generation, X-Definition cutting on mild steel, stainless steel and aluminum.
Industry Leading Cut Quality
- Consistent ISO range 2 results on thin mild steel
- Extended ISO range 3 cut quality results compared with earlier plasma technology
Optimized Productivity and Reduced Operating Costs
- Consumable life increases of over 40% compared with previous systems
- 20% thicker piercing capability on stainless steel and 30% thicker on mild steel
- Operating costs reduced by over 50%
The Whitney XPR170 package includes:
- XPR170 Plasma Power Unit
- Core™ Gas Console – for unmatched mild steel cutting performance and superior angularity and edge finish on stainless steel up to 12 mm (1/2″). This is delivered through a new N2 HDi™ process that prevents the mixing of air into the plasma gas, creating an improved, brighter edge finish.
- Optimix™ Gas Console (optional) – provides additional inputs and control for enhanced plasma processes in stainless steel and aluminum
- EasyConnect™ torch lead and one hand torch-to receptacle connection for fast and easy change-outs
- Whitney QuickChange positioning assembly for correct stand-off height
- Air Intensifier
- Dust Collector with filters and spark trap
- Robust Slag Collection System
XPR300 PLASMA CUTTING SYSTEM W/ CORE™ or OPTIMIX™ CONSOLE (OPTIONAL)
The Hypertherm XPR300™ Plasma Cutting System option is available in lieu of the standard MAXPRO200® plasma system.
The new XPR300™ represents the most significant advance in mechanized plasma cutting technology, ever. This next generation system redefines what plasma can do by expanding its capabilities and opportunities in ways never before possible. With unmatched X-Definition™ cut quality on mild steel, stainless steel and aluminum, the new XPR300 increases cut speed, dramatically improves productivity and slashes operating costs by over 50%. Newease-of-use features and engineered system optimization make the XPR300 easier to run with minimal operator intervention, while also ensuring optimal performance and unmatched reliability.
Advantages include:
The XPR advances HyDefinition® cut quality by blending new technology with refined processes for next generation, X-Definition cutting on mild steel, stainless steel and aluminum.
Industry Leading Cut Quality
- Consistent ISO range 2 results on thin mild steel
- Extended ISO range 3 cut quality results compared with earlier plasma technology
Optimized Productivity and Reduced Operating Costs
- 300 amps and 63 kW of output power deliver higher cut speeds; up to 15% on thicker materials
- Consumable life increases of over 40% compared with previous systems
- 20% thicker piercing capability on stainless steel and 30% thicker on mild steel
- Operating costs reduced by over 50%
The Whitney XPR300 package includes:
- XPR300 Plasma Power Unit
- Core™ Gas Console – for unmatched mild steel cutting performance and superior angularity and edge finish on stainless steel up to 12 mm (1/2″). This is delivered through a new N2 HDi™ process that prevents the mixing of air into the plasma gas, creating an improved, brighter edge finish.
- EasyConnect™ torch lead and one hand torch-to receptacle connection for fast and easy change-outs
- Whitney QuickChange positioning assembly for correct stand-off height
- Air Intensifier
- 12 Cartridge Dust Collector with filters and spark trap
- Robust Slag Collection System
BEVEL CUTTING HEAD FOR PLASMA CUTTING (OPTIONAL)
3-axis bevel cutting head integrated with the CNC control. The bevel head is supplied in lieu of the standard plasma cutting head.
The bevel head includes:
- Innovative light weight bevel design
- 95o Side-Side & 95o Forward-Back motion and 360o Full Rotation without twisting any cables or hoses!
- Eliminates the need for double handling. Cut steel and perform the weld preparation at the same time.
- Fixed tool center point eliminates translation adjustments
- Plasma torch movement is provided by digital drive amplifiers and servo motors for all axis – tilt, rotation and vertical height
- Arc voltage automatic height control to provide the most accurate bevel tolerance.
- Robust design for heavy industrial environment
- Consistent and reliable bevel quality for holes and edges
ADDITIONAL DUST COLLECTOR FOR PLASMA CUTTING ALUMINUM (OPTIONAL)
NOTE: ALUMINUM DUST CAN CAUSE FIRES OR EXPLOSIONS
The ADDITIONAL DUST COLLECTOR FOR PLASMA CUTTING ALUMINUM is a second dust collector that collects aluminum and steel in different dust collectors. The dust collector used for aluminum cutting must be located outside. Precautions must be taken when running aluminum. The chances for fires or explosions increase when running both steel and aluminum on the same machine. Hot steel slag (which has a higher melting point than aluminum) will ignite the aluminum dust particles.
The following items are included in the dust collector assembly:
- Dust collector and filters with silencer
- Explosion vent on dust collector (should there be an explosion, this will direct the force of an explosion in the appropriate direction, and minimize damage to the dust collector).
- Second slag pan, to be used for aluminum cutting only. This slag pan will be interlocked to make sure the appropriate slag pan is used (per part program).
- Manual damper vent to direct exhaust to the appropriate dust collector. This damper vent will be interlocked to make sure that the appropriate dust collector is selected per part program.
- Miscellaneous electrical components and software.
- Special ducting to prevent the settling of aluminum dust within the duct work.
- Documentation (manuals) and name plates
HIGH TEMPERATURE PACKAGE (OPTIONAL)
The HIGH TEMPERATURE PACKAGE includes extra cooling for the hydraulics and electrical when the standard environmental conditions cannot be met.
MACHINE ACCESSORIES
TOOL CADDY TOOLING EXPANSION SYSTEM (OPTIONAL)
The Tool Caddy automatically exchanges tools between the Rail Tool Changer and a rotary table, expanding the tool capacity from 12 stations to 33 stations. It includes 21 additional Tooling Cartridges and Tooling Adapter Assemblies for a total of 33.
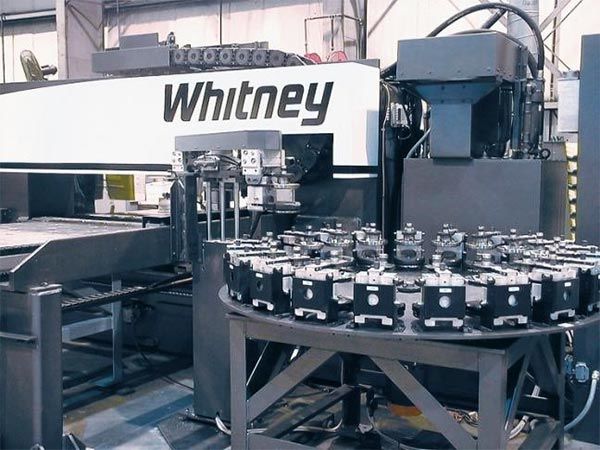
INK JET PART MARKING SYSTEM (OPTIONAL)
The INK JET PART MARKING SYSTEM provides a non-contact system to marks parts being produced on the machine. The sy