The Whitney 657CNC Combination Machine Tool uses the fastest technologies to make parts – Punching and Plasma Cutting.
- Punched holes provide accurate internal features.
- It is faster to punch holes than to pierce and contour holes with plasma or LASER.
- External features are plasma cut. Advanced plasma-cutting technology provides highly productive contouring (much faster than laser) with high quality.
- Small kerf angle (vertical cuts)
- Dross-free cutting
- Additional features such as forming (countersinks, tread plate, louvers), drilling and tapping can be added to eliminate additional downstream operations, allowing parts to be completed in a single operation.
Manufacturing costs are lower using the combination machine technology.
- Labor costs are lower because it takes significantly less time to manufacture the parts.
- Operating costs are lower.
- Amortization of capital costs is significantly lower since
- Lower initial capital cost than LASER
- Faster cycle time – Cost of capital per fabricated part is lower because capital costs are amortized over more fabricated parts.
The PROFIT-DOUBLER
- Higher profit per part —lower overall cost per piece gives a higher profit margin per piece.
- More parts generating profit—more parts are produced (in the same amount of time) on a combination machine, so there are more parts generating profit than on the other technologies.
SPECIFICATIONS OF MODEL 657CNC
|
METRIC |
INCH |
PUNCHING FORCE |
360 kN |
40 Tons |
MAXIMUM PUNCH SIZE |
127 mm |
5.000″ |
PUNCHING HIT RATE |
80 hits per minute |
80 hits per minute |
X-AXIS TRAVEL |
920 mm |
75.50″ |
Y-AXIS TRAVEL |
1250 mm |
49.20″ |
POSITIONING ACCURACY |
±0.12 mm |
±0.005″ |
NOMINAL DISTANCE BETWEEN PUNCH & TORCH
(X-AXIS) |
381 mm |
15.0″ |
RAPID SPEED PER AXIS |
25.4 M/min |
1,000 in/min |
PUNCHING STROKE LENGTH |
25.4 mm |
1.000″ |
TOOLING STYLE |
Piranha 28XX |
Piranha 28XX |
MAXIMUM WORKPIECE WEIGHT |
225 kg |
500 lb |
MINIMUM WORKPIECE THICKNESS |
1.5 mm |
0.060″ |
MAXIMUM WORKPIECE THICKNESS |
12.7 mm |
0.500″ |
WORK CLAMP OPENING |
16 mm |
0.625″ |
MINIMUM WORK CLAMP SPREAD |
150 mm |
6.0″ |
MAXIMUM WORK CLAMP SPREAD |
1320 mm |
52.0″ |
PLASMA CUTTING SYSTEM |
Hypertherm HSD130 |
Hypertherm HSD130 |
PLASMA TORCH HEIGHT CONTROL SYSTEM |
Hypertherm Sensor PHC |
Hypertherm Sensor PHC |
CNC CONTROL |
Piranha |
Piranha |
INCLUDED EQUIPMENT
This proposal describes the Model 657 Combination Plasma Punch Machine Tool, 40 ton (360 kN) capacity, 49.2″ x 75.5″ (1250 mm x 1920 mm) positioning area, per attached specifications, for 460/3/60 volt incoming power.
Included as standard equipment:
Piranha Positioning / Contouring Control
- 15” (380mm) Touch screen CNC control
- Windows XP operating system
- 32 Gb SSD Hard Drive – available for part program storage
- 15 Mb maximum part program size
- Graphics display
- Integrated parametric shape library
- RJ45 Ethernet connection for networking and remote diagnostics capability
Punching and Forming
- ‘C’ frame design with open throat
- Electronic stroke control
- Positive stripping
- Pressure switch for forming and marking
- Manual punch and die locking system
- 28XX tooling system
- Slug collection pan
Integrated Plasma System and Support Equipment
- Hypertherm HSD130 plasma cutting system
- Sensor PHC torch height control
- Water cooled slag chamber
- Dust collector and spark trap
Hydraulic Work Clamp Assemblies
- (2) work clamps with variable locations
- 1,500 PSDI (6.6 kN) clamping force per clamp
- Replaceable work piece locators
Programmable Repositioning Assembly
Hydraulic Power Unit, with 15 hp (11kw) motor and hydraulic oil.
Remote Diagnostics Package – allows many machine problems to be diagnosed via the Internet using TeamViewer. Piranha Service Technicians can log directly onto the CNC control for the purpose of diagnosing problems, reviewing NC programs, downloading new software, and changing parameters if required. Customer is responsible for providing a suitable Ethernet connection at the machine CNC control with Internet access. A telephone line or cell phone is recommended so that the technician can talk to the operator/maintenance person while diagnosing the problem.
Software License for all software resident on the CNC Control. The software is proprietary, and the intellectual property of Piranha. Prior to the commissioning of the machine tool, the user must sign a software license agreement. This is a non-transferable license that must be renewed by any and all subsequent owners of the machine tool. The value of this software license is $1,500.00, and it is included in the price of the machine.
Electrical Standards – The machine conforms to Piranha electrical design standards which are based on N. E. C., NFPA-79, and UL Standards with deviations. Components are NEMA and IEC rated where possible.
40 TON PUNCHING CAPACITY (STANDARD)
The 40 TON PUNCHING CAPACITY allows the 657CNC to:
- Punch larger hole sizes in a given material type and thickness
- Punch holes in higher tensile strength materials
- Punch thicker materials
IMPORTANT NOTE: Punching of high tensile material is a special application for Piranha Combination Machine Tools and may void the machine warranty and cause premature tooling wear. High tensile strength material is defined as any material whose tensile strength is greater than 60ksi (413 MPa). Materials often referred to as “remnants” or “seconds” will often randomly exhibit tensile strength greater than 60ksi (413 MPa) and thus will void the machine’s warranty. PIRANHA reserves the right to have a representative sample of customer supplied material mechanically and/or chemically tested. If processing high tensile material, please consult the factory for a review of your specific requirements. In some cases, a larger Piranha Combination Machine model could be recommended.
HSD130 PLASMA CUTTING SYSTEM (STANDARD)
The Hypertherm™ HSD130 Oxygen Plasma Cutting System offers LongLife® Oxygen Parts Technology, giving high quality plasma cuts with excellent consumable life. Advantages of the HSD130 system include the following:
- Little or no dross on plasma cut edges
- Excellent contour definition (achieved due to a minimized “arc lag”)
- Long consumable life – between 500 and 1200 starts per set of consumables
- Improved kerf angle
- Exceptional surface finish
Amperage Range
45 – 130 amps (Process dependent)
Gases Required
Oxygen
- 99.5% pure (liquid recommended)
- 115 psi (7.93bar), at 150 scfh (4250 l/h)
- Clean, dry, oil-free
Air
- 95 psi (6.55 bar) at 300 scfh (8500 l/h)
- Clean, dry, oil-free
Nitrogen
- 99.99% pure
- 120 psi (8.3 bar) at 80 scfh (2265 L/h)
- Clean, dry, oil-free
H35 Argon/Hydrogen
- H35 = 65% Argon, 35% Hydrogen
- 99.995% pure
- 115 psi (7.93 bar) at 150scfh (4250l/h)
F5 Nitrogen/Hydrogen
- F5 = 95% Nitrogen, 5% Hydrogen
- 99.98% pure
- 115 psi (7.93 bar) at 150scfh (4250l/h)
NOTE: Customer is to furnish suitable regulators for all supply gas connections.
Process Selections
The HSD130 can cut with a variety of plasma gases and shield gases. Selection of the cutting process depends upon speed, quality, and cost requirements, and is the responsibility of the user.
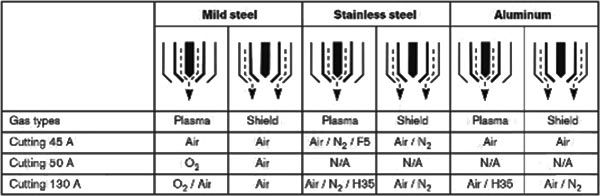
Plasma Arc Cutting Speeds
The charted/published values for the HSD130 Oxygen Plasma Cutting System represent the speeds attainable under controlled conditions. The practical speeds without prior testing for running “short runs” of low-carbon steels will be as follows. This represents the optimum production values for minimum setup procedure/time and best quality cuts (and largest operating window).
Cutting Speeds – HSD130
Mild Steel
CURRENT PLASMA/SHIELD |
.075″ 2.0 MM |
.135″ 3.0 MM |
.187″ 4.0 MM |
.250″ 6.0 MM |
.375″ 10.0 MM |
.500″ 12.0 MM |
45A AIR/AIR |
235 IPM
5.80 MPM |
90 IPM
3.30 MPM |
|
|
|
|
50A, O2/AIR |
220 IPM
5.40 MPM |
130 IPM
3.65 MPM |
|
|
|
|
130A AIR/AIR |
|
220 IPM
6.00 MPM |
160 IPM
4.93 MPM |
150 IPM
3.85 MPM |
100 IPM
2.45 MPM |
75 IPM
2.05 MPM |
130A
O2/AIR |
|
240 IPM
6.50 MPM |
190 IPM
5.42 MPM |
150 IPM
4.00 MPM |
110 IPM
2.65 MPM |
80 IPM
2.20 MPM |
Machine Options
657 DIE ADAPTERS AND STRIPPERS
Strippers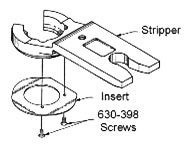
Minimum Diameter |
Maximum Diameter |
Maximum
Work Piece
Thickness |
Use Whitney Part Number(s) |
Included |
Not Included |
— |
0.812″ 20.6 mm |
0.125″
3 mm |
630-287 Stripper* 636-306 Insert* |
X |
|
0.250″
6 mm |
630-287 Stripper |
X |
|
0.500″ 12.7 mm |
806-613 Stripper |
X |
|
0.812″ 20.6 mm |
1.437″ 36.5 mm |
0.125″
3 mm |
630-286 Stripper* 636-307 Insert* |
X |
|
0.250″
6 mm |
630-286 Stripper |
X |
|
0.500″ 12.7 mm |
807-797 Stripper |
X |
|
1.437″ 36.5 mm |
2.000″ 50.8 mm |
0.125″
3 mm |
630-285 Stripper* 636-308 Insert* |
|
X |
0.250″
6 mm |
630-285 Stripper |
|
X |
0.500″ 12.7 mm |
813-179 Stripper |
|
X |
2.000″ 50.8 mm |
3.000″ 76.2 mm |
0.125″
3 mm |
630-284 Stripper 636-309 Insert |
|
X |
0.250″
6 mm |
630-284 Stripper |
|
X |
3.000″ 76.2 mm |
4.000″ 101.6 mm |
0.125″
3 mm |
630-283 Stripper 636-310 Insert |
|
X |
0.250″
6 mm |
630-283 Stripper |
|
X |
4.000″ 101.6 mm |
5.000″ 127.0 mm |
0.125″
3 mm |
808-051 Stripper 636-311 Insert |
|
X |
0.250″
6 mm |
808-051 Stripper |
|
X |
* Urethane stripper sleeves can be used in lieu of mechanical strippers |
Die Adapters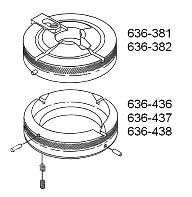
Part Number |
Inside Diameter |
Fits Die Sizes** |
Included |
Not Included |
636-381 |
1.250″ 31.75 mm |
Up to 0.824″ Up to 20.93 mm |
X |
|
636-382 |
2.125″ 53.98 mm |
0.825″ – 1.465″ 20.94 mm – 37.21 mm |
X |
|
636-436 |
2.750″ 69.85 mm |
1.466″ – 2.012″ 37.22 mm – 51.50 mm |
|
X |
636-437 |
3.750″ 95.25 mm |
2.013″ – 3.012″ 51.51 mm – 76.50 mm |
X*** |
|
636-438 |
4.750″ 120.65 mm |
3.013″ – 4.012″ 76.51 mm – 101.90 mm |
|
X |
** Round die sizes. See Piranha Tooling Catalog for other shape. |
|
|
*** Required for punch and die alignment procedure. |
|
|
HYDRAULIC PUNCH LOCK (OPTIONAL)
The HYDRAULIC PUNCH LOCK option replaces the manual punch lock adapter with a unique air/hydraulic system. A machine mounted switch locks or unlocks the punch for faster tool change cycle times.
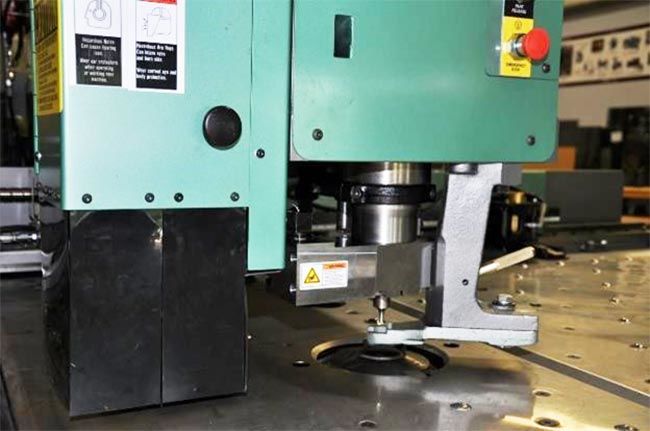
CAM PROGRAMMING AND NESTING SOFTWARE
CNC Programming of the Piranha 657CNC requires CAM software capable of supporting the advanced functions of the machine. The customer is responsible for all costs associated with the development of any new post processor from their selected CAM software vendor. Piranha will provide any information required for the post processor development and will verify that the NC code samples created by that post processor are functional. Requests for information and NC code samples for testing must be received by Piranha eight (8) weeks prior to the scheduled machine shipment.
If extra start-up time is required by Piranha to work with the CAM provider and to test the NC code during or after the machine installation, the additional Piranha service time and expenses will be invoiced to the customer at Piranha’s standard service rates.
INSTALLATION
Installation is included with the machine purchase.
TRAINING
Training will take place at the time of installation and will cover the operation of the machine, best practices for programming and applications, and basic preventive maintenance. All programmers, shift operators, and maintenance personnel for the machine are asked to participate in this training.
A follow-up visit by a factory representative will occur within six (6) weeks of the completion of the installation. During this time, the Buyer may receive additional training in applications, operation, or maintenance as required at no additional charge.
WARRANTY
Warranty period is one (1) year.
PHONE SUPPORT
Phone support will be provided for the life of the machine at no additional charge.
BUDGETARY PROPOSAL
This budgetary proposal is a reference document and subject to change without notice. Upon request, a final proposal will be issued including firm pricing and contractual information. This budgetary proposal is not an agreement on pricing or specifications.