Piranha P-90 Ironworker
The 90 Ton Piranha Model P-90 picks up where the Piranha P-65 Ironworker leaves off – for applications requiring more tonnage.
- The P-90 has more standard workstations than any other ironworker in its class. This includes punching, bending, bar shear, angle shear, round bar shear, and an integrated coper/notcher.
- The P-90 also has a dovetail slide that allows an operator to switch from punching to bending in just a few seconds.
- The P-90 has full electrical control of its stroke with a footswitch and limit switch stroke controls.
- The no slug-loss shearing saves material, keeps the machine area cleaner, and offers larger material capacity than the competition. A wide variety of optional tooling is available to enhance the P-90’s capabilities.
- Piranha’s incomparable integrated coper/notcher station outperforms any other ironworker. Notch from thick to thin, remove the full leg from angle iron, shave even the smallest piece from the end of the work piece, and maintain total control of the part – from any angle.
Ironworker Machine Build and Testing
Piranha Ironworker Machine Build and Testing Process
STANDARD FEATURES
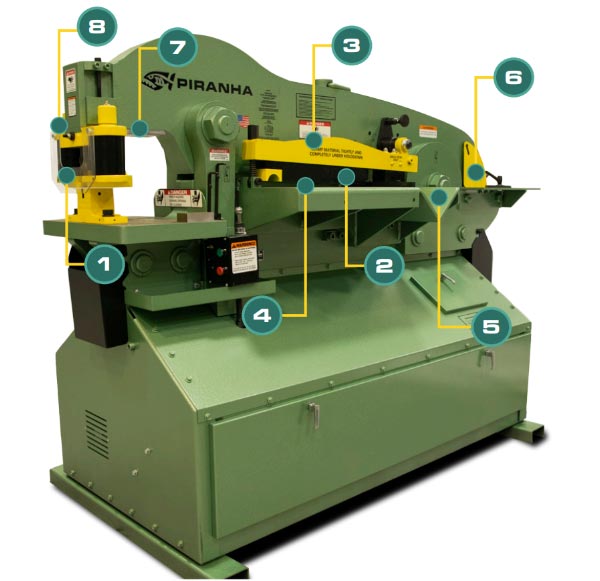
P-65 Model Pictured Here
- Urethane Stripper Attachment- keeps material flat through the punching process, eliminating
distortion. The shorter required stroke gives you a faster punching cycle.
- Automatic Urethane Hold-downs- clamps and releases material automatically with each stroke. Part movement is eliminated by clamping the part throughout the entire shearing cycle.
- 3. Visibility- a direct line of sight over the hold down bar allows the operator to easily and accurately line up cuts to the shear blades.
- Flat Bar Shear- the low rake angle shear design results in flatter and higher quality sheared parts. Shear blades have four useable edges giving you a longer life and less expensive blades.
- Angle Shear- the floating upper blade seats in the center of the angle prior to cutting minimizing
distortion giving you a higher quality cut.
- Coper Notcher- the low rake angle keeps part flat and under control during notching.
- Quick Change Tooling– the unique Piranha dovetail design allows for quick installation and removal of all standard and optional tools.
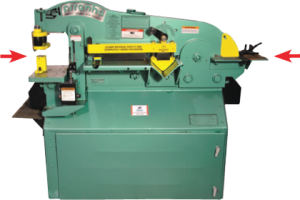
Piranha work stations are at a consistent, ergonomic level throughout the entire machine. Easily adaptable to material feed systems without the need to adjust the height between stations.
MAXIMUM SPECIFICATIONS (rated on mild steel)
Punching (90 Tons) |
1-1/8” diameter through 1” plate |
Throat Depth |
10” |
Bending (Optional) |
12” up to 24” w/4-way die block |
Round Bar Shear |
1/2” through 2” |
Square Bar Shear |
1/2” through 1-3/8” |
Flat Bar Shear |
18” x 1/2”, 12” x 3/4”, 8″ x 1″ |
Angle Shear |
5” x 5” x 1/2” |
Coping/Notching |
3-1/2” x 5” x 1/2” |
Motor |
10 HP |
Weight |
4,250 Lbs. |
STANDARD EQUIPMENT
- Automatic Hold Down
- Coupling Wrench
- Punch Holder, Stripper, & Die Block
- 3/8” Allen Wrench
- 5 Punch & Die Sets 9/16” through 1-1/16”
- Set of Chip Buckets
- Set of Angle Knives
- Extra Filter Element
- Set 1-1/4” Round Bar Knives
- Foot Switch
- Set of 14-5/8” Plate Shear Knives
- Instruction/Parts Book/Video Link
- Set of Coper Knives
ATTACHMENTS
BENDING ATTACHMENTS
The bending attachments are designed to increase productivity on the punch end of the machine. They utilize the dovetail mounting system for quick and easy installation. The 8”, 12” and 14” versions are mounted parallel to the beam allowing you unlimited throat depth and the 24” version mounts perpendicular to the beam. All bending attachments include 4-way bending dies with openings of 7/8”, 1-1/8”, 1-1/2” and 2”.
CHANNEL PROCESSING ATTACHMENTS
On the punch end of the machine we offer an adjustable Channel Shear capable of shearing 2”-8” standard channel. We also offer a Channel Die Block which replaces the standard die block and is designed to punch a hole in the leg or web of channel.
OVERSIZE PUNCHING ATTACHMENTS
Oversize Attachments mount in place of standard punch attachment and are designed to punch a 50-ton maximum hole. Heavy Duty attachments and urethane stripping options for attachments 2-3/4” and larger are available upon request.
QUICKSET GAUGING TABLES
The quickset gauging table option is a productivity tool for the punch end. The gauging table mounts around the die block and uses finger stops to repeat a series of punched holes in flat bar or angle. The attachment comes with a table and flat bar gauge with measuring rules for easy hole location layout. A 5’ or 10’ extension can be added to the left or right side of the base table for longer part processing.
SHEARING BACKGAUGES
The backgauge option is a productivity tool for the shearing section. The backgauge mounts on the drop side of the machine and uses a compression sleeve for infinite, easy adjustment to gauge cut lengths in the angle, flat bar and round bar shearing stations. Electronic versions of this backgauge are available which automatically cycles the machine every time material makes contact with the backgauge probe. A support leg is included with the 9’ and 12’ versions.
ROLLER FEED TABLES
The roller feed tables come in 5’ lengths and can be bolted together to make longer sections for fast, easy feeding of plate or angle. Includes 20” wide rollers for flat bar and 6” rollers in the angle section. Adjustable to accommodate floor height and machine type.
PIPE NOTCHING ATTACHMENTS
The pipe notching attachments mount easily on the platen table in place of the punch die block. This is a single notch system. To notch both sides of the pipe you must rotate the pipe and realign with the notching die for the second notch.
The pipe notching attachment is made up of three separate pieces, the pipe notching die holder, the pipe notching die and the pipe notching striker.
- The pipe notching die holder is a universal die holder that bolts to the platen table and can accept 3/4” through 2” Schedule 40 Pipe Notching Dies
- The pipe notching dies are spring return die sets that mount in the pipe notching die holder. Standard sizes of pipe notching dies are 3/4”, 1”, 1-1/4”, 1-1/2” and 2” Schedule 40. Other sizes of pipe and tube notching dies are available upon request but may require a different die holder.
- The pipe notching striker is an extended flat bottom punch used in your standard stripper assembly to press down the pipe notching die.
Learn More About Available P-90 Machine Attachments
DELIVERY
Normal delivery is from stock subject to confirmation at the time of order. Price is ExWorks factory Rockford, Illinois and does not include any applicable sales tax or installation. Up to twenty-five gallons of ISO Grade 32 hydraulic oil is required. The machine is shipped totally wired through the electrical enclosure box. It has been left to the purchaser’s discretion whether to wire direct to a disconnect or to install a cord and plug for mobility.
SHIPMENT REQUIREMENTS
MegaFab requires Flatbed Trailer(s), with adequate Chains and tarps (to cover full height and width), to assure protection of this equipment when using truck transportation. Please make sure that adequate deck space is allotted for machine and all accessories shipping with order. Upon request, MegaFab will arrange shipping to destination. Freight and insurance charges are the responsibility of the customer, and will be invoiced on machine order. Please consult the factory for any questions regarding shipping requirements.
WARRANTY
Twelve (12) months, covering parts against defects in materials or workmanship.
Price and specs are subject to change without notice.